La industria minera es una de las más exigentes del mundo. Equipos, maquinaria y estructuras están constantemente sometidos a condiciones extremas, como temperaturas extremas, alta humedad, abrasión intensa y cargas pesadas. En este entorno desafiante, la soldadura juega un papel fundamental en la construcción, mantenimiento y reparación de los equipos utilizados en minería.
En este artículo, exploraremos la importancia de la soldadura en la industria minera, los métodos más eficientes, las innovaciones tecnológicas y las mejores prácticas para garantizar uniones resistentes y duraderas.
La importancia de la soldadura en la minería
La minería requiere equipos robustos capaces de resistir condiciones adversas durante largos períodos. La soldadura permite la fabricación y mantenimiento de componentes clave, asegurando su rendimiento óptimo y reduciendo costos de reparación.
Beneficios de una soldadura resistente en la industria minera:
-
Mayor vida útil de los equipos: Reduce el desgaste prematuro y las fallas mecánicas.
-
Resistencia a la abrasión y corrosión: Asegura que las estructuras y equipos soporten ambientes hostiles.
-
Eficiencia operativa: Reduce tiempos de inactividad debido a reparaciones.
-
Cumplimiento de normativas de seguridad: Garantiza la estabilidad de estructuras y maquinaria.
Según la American Welding Society (AWS), más del 80% de las fallas en equipos de minería se deben a uniones soldadas defectuosas o mal ejecutadas, lo que resalta la importancia de aplicar técnicas adecuadas y controles de calidad rigurosos.
Métodos de soldadura más utilizados en minería
1. Soldadura por arco metálico con gas (GMAW/MIG)
-
Utiliza un electrodo de alambre continuo y gas protector.
-
Alta productividad y buena penetración en materiales gruesos.
-
Ideal para reparaciones rápidas y fabricación de componentes estructurales.
2. Soldadura por arco con electrodo revestido (SMAW)
-
No requiere gas protector, ideal para trabajos en campo.
-
Se adapta a diversas condiciones ambientales extremas.
-
Comúnmente utilizada en la reparación de maquinaria pesada y estructuras metálicas.
3. Soldadura por arco de tungsteno con gas (GTAW/TIG)
-
Alta precisión en uniones soldadas.
-
Utilizada en la fabricación de componentes críticos y materiales especiales.
-
Ideal para aleaciones resistentes a la corrosión.
4. Soldadura por arco sumergido (SAW)
-
Proceso automatizado con alta penetración.
-
Usado en la fabricación de estructuras de acero de gran tamaño.
-
Reduce defectos y mejora la calidad de las uniones.
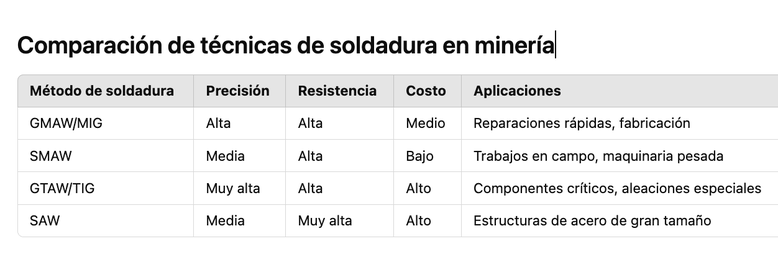
La tabla muestra una comparación de cuatro técnicas de soldadura distintas, evaluando su precisión, resistencia, costo y aplicaciones comunes en la industria minera.
Técnicas de soldadura:
- GMAW/MIG (Soldadura por arco metálico con gas): Es un proceso de soldadura por arco que utiliza un electrodo consumible continuo y un gas de protección.
- SMAW (Soldadura por arco metálico protegido): También conocida como soldadura con electrodo revestido, utiliza un electrodo consumible recubierto con fundente.
- GTAW/TIG (Soldadura por arco de tungsteno con gas): Utiliza un electrodo de tungsteno no consumible y un gas de protección para producir soldaduras de alta calidad.
- SAW (Soldadura por arco sumergido): Es un proceso de soldadura por arco donde el arco y el metal de soldadura fundido están cubiertos por un manto de fundente granular.
Análisis de la tabla:
-
Precisión: El método GTAW/TIG destaca por su precisión muy alta, seguido por GMAW/MIG con alta precisión. SAW y SMAW tienen una precisión media.
-
Resistencia: SAW ofrece la resistencia más alta, seguido por GMAW/MIG y GTAW/TIG que ofrecen alta resistencia. SMAW ofrece una resistencia media.
-
Costo: GTAW/TIG y SAW tienen un costo alto, GMAW/MIG tiene un costo medio y SMAW es el más económico.
Aplicaciones:
- GMAW/MIG: Se utiliza comúnmente en reparaciones rápidas y fabricación de equipos y estructuras en la minería, donde se requiere un equilibrio entre velocidad, precisión y costo.
- SMAW: Se utiliza en trabajos en campo y soldadura de maquinaria pesada, ya que es un método versátil y fácil de usar en diferentes condiciones ambientales y posiciones de soldadura, lo cual es crucial en entornos de minería remotos y de difícil acceso.
- GTAW/TIG: Se utiliza en la soldadura de componentes críticos y aleaciones especiales, donde la calidad y precisión de la soldadura son fundamentales, como en la fabricación o reparación de equipos de alta tecnología o componentes sometidos a condiciones extremas.
- SAW: Se utiliza en la soldadura de estructuras de acero de gran tamaño, como en la construcción de plantas de procesamiento o en la fabricación de grandes componentes estructurales.
Cada técnica de soldadura se adapta a diferentes necesidades en la industria minera, considerando factores como la precisión requerida, la resistencia estructural necesaria, el costo y las aplicaciones específicas. La elección de la técnica adecuada dependerá de las características particulares del proyecto, incluyendo el tipo de material, las condiciones ambientales, la ubicación del trabajo y el presupuesto disponible.
Es importante tener en cuenta que esta tabla es una simplificación y otros factores, como el espesor del material, la accesibilidad de la junta, las normativas de seguridad en la minería y la disponibilidad de equipos y personal calificado, también pueden influir en la selección de la técnica de soldadura.
Factores clave para una soldadura eficiente en minería
-
Selección del material adecuado: Asegurar que los metales base y de aporte sean compatibles con las condiciones extremas.
-
Control de temperatura y deformaciones: Aplicar técnicas de precalentamiento y post-enfriamiento para evitar grietas y defectos.
-
Inspección y pruebas de calidad: Uso de ensayos no destructivos (END) para verificar la integridad de las uniones soldadas.
-
Capacitación del personal: Soldadores especializados garantizan mejores resultados y reducen errores.
-
Uso de equipos de última generación: Máquinas de soldadura con tecnología avanzada mejoran la precisión y durabilidad de las uniones.
Innovaciones tecnológicas en soldadura para minería
La soldadura ha evolucionado significativamente en los últimos años, introduciendo tecnologías que mejoran la eficiencia y calidad en el sector minero.
-
Soldadura robotizada: Reduce el error humano y mejora la precisión.
-
Sensores de monitoreo en tiempo real: Detectan defectos durante el proceso de soldadura.
-
Soldadura láser: Proporciona uniones extremadamente resistentes y de alta precisión.
-
Uso de inteligencia artificial: Algoritmos optimizan los parámetros de soldadura en tiempo real.
Normativas de soldadura en la industria minera
La minería es un sector altamente regulado, y las soldaduras utilizadas en sus operaciones deben cumplir con normativas internacionales para garantizar la seguridad y eficiencia.
-
AWS D14.3/D14.3M: Soldadura para equipos de construcción y minería.
-
ISO 3834: Requisitos de calidad para procesos de soldadura.
-
ASME Sección IX: Códigos de calificación para procedimientos y soldadores.
-
API 1104: Especificación para la soldadura de tuberías en la industria petrolera y minera.
Casos de éxito en soldadura aplicada a la minería
1. Mina de Chuquicamata (Chile)
Uno de los yacimientos más grandes del mundo, donde la soldadura automatizada ha permitido reducir tiempos de reparación en maquinaria de alto tonelaje.
2. Mina de Peñasquito (México)
Uso de soldadura de alta resistencia en cintas transportadoras y equipos de perforación, minimizando el tiempo de inactividad y maximizando la producción.
3. Mina Grasberg (Indonesia)
Aplicación de soldadura especializada en estructuras de acero sometidas a condiciones climáticas extremas, garantizando su durabilidad.
Conclusión
La soldadura en la industria minera es un componente clave para garantizar la seguridad, resistencia y durabilidad de las estructuras y equipos en condiciones extremas. La implementación de técnicas avanzadas, el uso de materiales de alta calidad y la aplicación de tecnologías innovadoras permiten reducir costos operativos y mejorar la eficiencia de las operaciones mineras.
Invertir en soldadura de alta resistencia no solo prolonga la vida útil de los equipos, sino que también optimiza la productividad y asegura el cumplimiento de los estándares de seguridad más exigentes en el sector minero.